How automation can improve drone operations
Most inspections today still use drones that are controlled manually by one or two highly skilled pilots. Many pilots are freelancers, and they are also in demand. That means it can be a challenge to find capable pilots who:
- know about utilities to capture what you need at the right angles efficiently.
- have the skills required to not damage either the drone or the assets.
- are available when you need the work done.
Data capture
Productivity requires good quality data and good data starts with capturing the right data, at the right angles and from the right distance.
These challenges can be overcome if we automate the drones performing the data capture. In this way, it also becomes much easier to find pilots and scale operations without reducing the consistency and overall quality. Automated drones require pilots with a different skill set, that is focused on deploying drones on pre-programmed paths instead of flying them. Since there are more pilots with this skill set, you can easily scale your operations to larger volumes.
What is a flight profile?
A typical flight profile includes parameters such as altitude, speed, direction and camera orientation, as well as a specific flight path that the drone will follow to ensure complete coverage of the asset being inspected. The use of well-designed flight profiles is essential to ensure accurate and reliable data collection during drone-based asset inspections.
When automating data capture, you should consider what flight profile can deliver the most end-to-end productivity. Tell your service provider what aspects of the assets are of interest. Ask them how they ensure that the profile is optimized in relation to the two points below as these will influence end-to-end productivity:
- Number of fights required (assets per day)
- Number of images captured (images per asset)
Doing both will have a direct impact on how you define the project, requirements scope, and budget.
But, what are automated flights?
There are two types of automated flights: linear and orbit. It is very important to select the right type depending on your needs.
Linear flights can be used for small, less complex structures such as distribution systems.
However, for large complex systems such as transmission systems, the best option is using orbital flights. In the orbital scenario, drones circle around the asset, capturing both sides, the underneath and the diagonal. By capturing more images with the highest quality, you are securing the coverage you need. This means fewer flights and therefore increased productivity.
Automated orbital flights let you perform very complex inspections at scale.
What to consider when analyzing defects. An AI perspective.
Comprehensive, annotated, and relevant training data should be the starting point. In order to achieve good AI performance and therefore the associated productivity gains it can bring, drone collected data must be of a high enough quality and at a sufficient detail level to distinguish the geometric or textural details of the objects of interest.
To get the most from your AI analysis, you need to consider the type of defect you are looking for.
There are two types:
- Structural defects — for example, where there is a crack in an object, missing components or the presence of foreign objects.
- Surface defects — where the texture or surface of the object has been altered, for instance, due to corrosion or flashover.
For structural defects, the most important parameter is GSD. It enables you to assess the width, length, and shape of a defect or detect if a certain component is present or not.
For surface defects, the dynamic range of the image is important in order to assess the severity of the defect. Under-exposed images or images with shadows hiding the defect will limit the AI’s ability to analyze. Your AI needs to be able to see details.
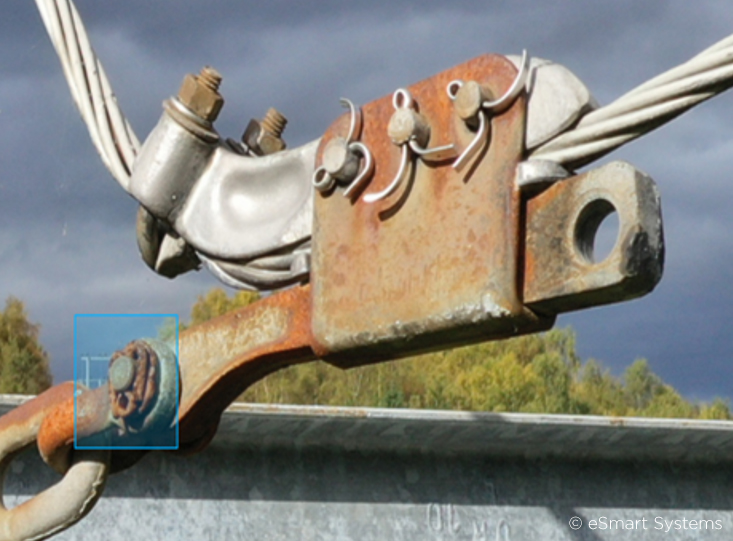
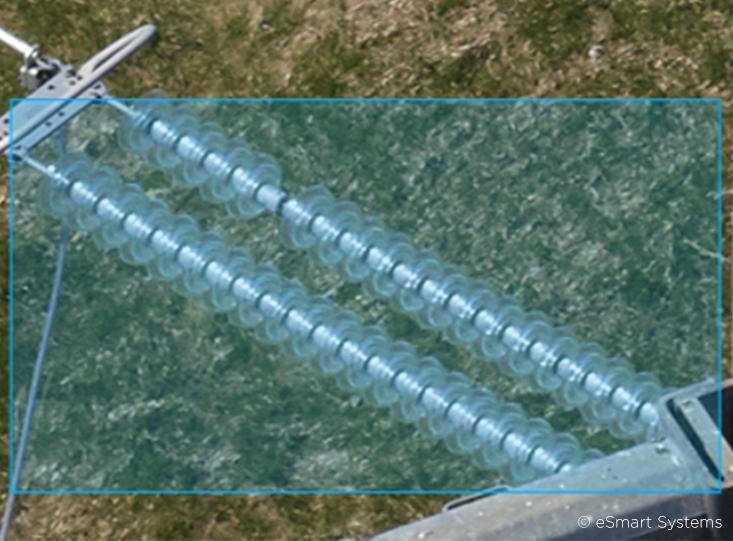
In summary, automating drone operations can significantly boost efficiency and scalability. Instead of relying on highly skilled manual pilots, automated drones following pre-programmed paths make it easier to find qualified operators and expand your operations. Choosing the right flight profile based on the complexity of the structures is key to increasing productivity. Combining these factors with high quality images and an AI-based defect analysis can be a game-changer for accurately spotting structural and surface defects, ensuring thorough and effective inspections.
Share this on social media: