The Challenge
Wind turbines need regular inspections to ensure their structural integrity. Until now, this has been done with manual inspections or drone inspections with lower-resolution cameras.
These methods usually require stopping the turbine, resulting in over an hour of lost operational time, or up to 6000 Euros in lost energy production. They also require personnel to be on site to control each turbine.
Capturing clear, detailed images while turbines are in motion requires maintaining safe distances from the blades without compromising image quality. In turn, this requires drone stability in the high-wind conditions typically found at wind turbine sites.
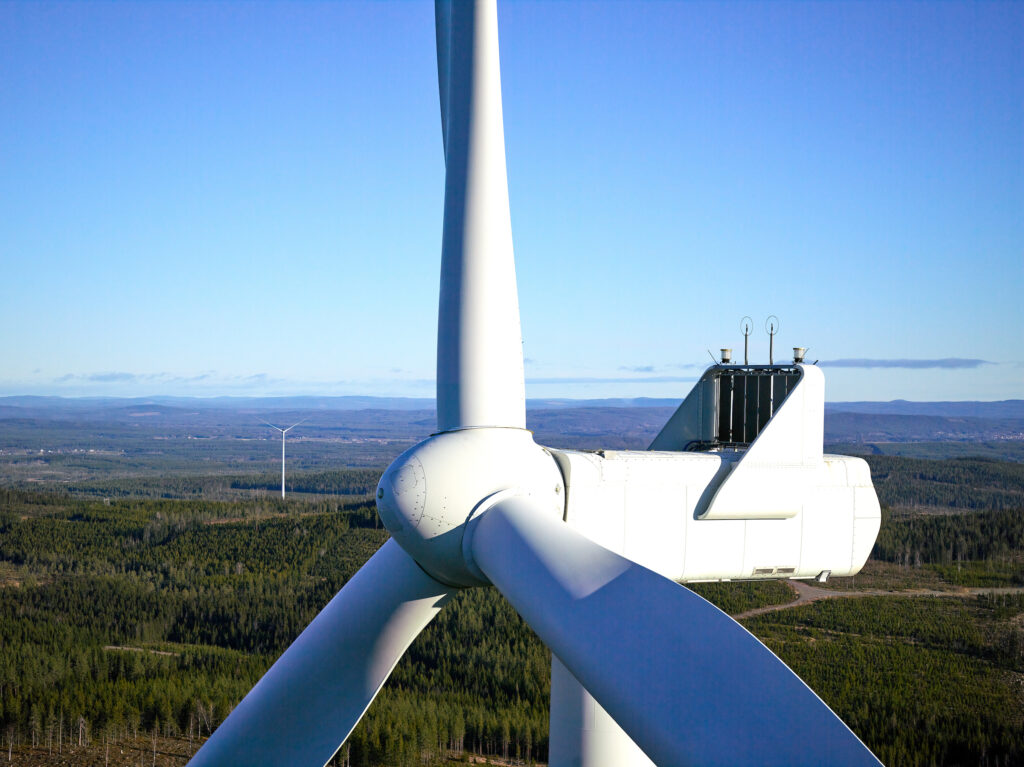
Surveying Is Currently Laborious
To survey a blade, a technician needs to be on site and needs to stop the turbine at the right position – with the selected blade at 12 o’clock – before calibrating and beginning their imaging work.
Due to the limitations of the sensors typically used in UAVs, they need to fly very close to the blade, at just 3 to 5 meters away.
Using a semi-automated Flight Pattern, UAVs follow a pre-set flight path around the stationary turbine to capture images of one blade at a time. Once one blade is inspected, the turbine must be rotated to position the next blade for inspection. Typically, this means setting the blade to the 12 o’clock position. If parts of a blade are missed during the survey, the entire inspection for that blade must be restarted.
This approach is very time consuming, as each complete blade inspection cycle, including rotating the turbine, can take up to an hour. During this time, the turbine must remain stationary, leading to downtime.
Using a fully automated option, this eliminates the need to rotate blades between inspections. The UAVs or integrated systems can inspect all three blades in one session. It is still required to set one blade to the 12 o’clock position initially, ensuring a proper calibration or starting point.
The advantages are clear: A significant reduction in downtime and faster overall inspection processes. In addition, companies benefit from reduced operational complexity as there’s no need to rotate the turbine between blades. Fully automated systems may require advanced UAVs, software, and calibration, which can be more expensive initially.
In summary, semi-automated systems may still be suitable for smaller operations or specific use cases, while fully automated systems offer efficiency for high-volume or large-scale inspections.
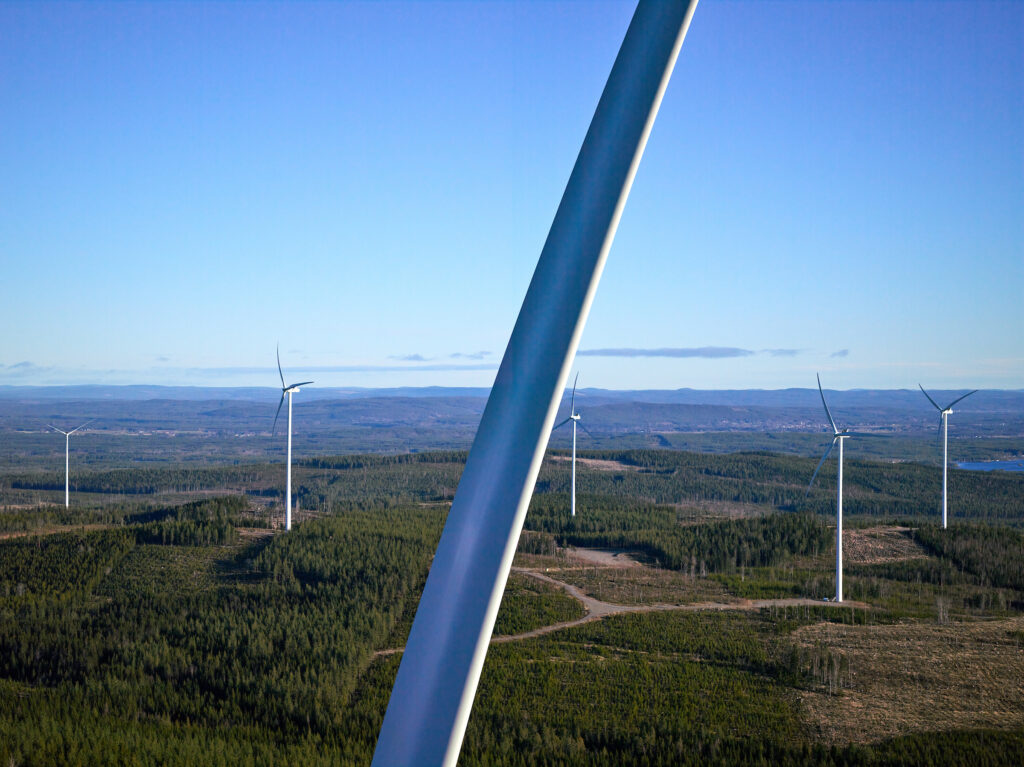
Enter High-Resolution UAV Surveying
To capture high-resolution images of wind turbine blades while they are in motion, the team at Drone Solution sought a solution for inspecting turbines from 60 meters’ distance. This would ensure the safety of personnel and avoid accidentally hitting the moving blades.
Drone Solution wanted the unparalleled image clarity and stability that Phase One provides.
“We chose Phase One for their high resolution, durability, and adaptability in industrial inspection environments,” says Drone Solution’s Jorge Ramos.
They selected a Phase One P3 payload: an iXM-GS120 camera with an 80mm lens. The P3 iXM-GS120 is known for its ability to deliver clear, precise images at greater distances, making it suitable for safe, efficient inspection of moving turbines.
The team integrated the P3 iXM-GS120 with a DJI Matrice 350 UAV. Integration was smooth with a few adjustments necessary to ensure stable positioning and consistent angle capture, to meet the unique demands of moving turbine inspections.
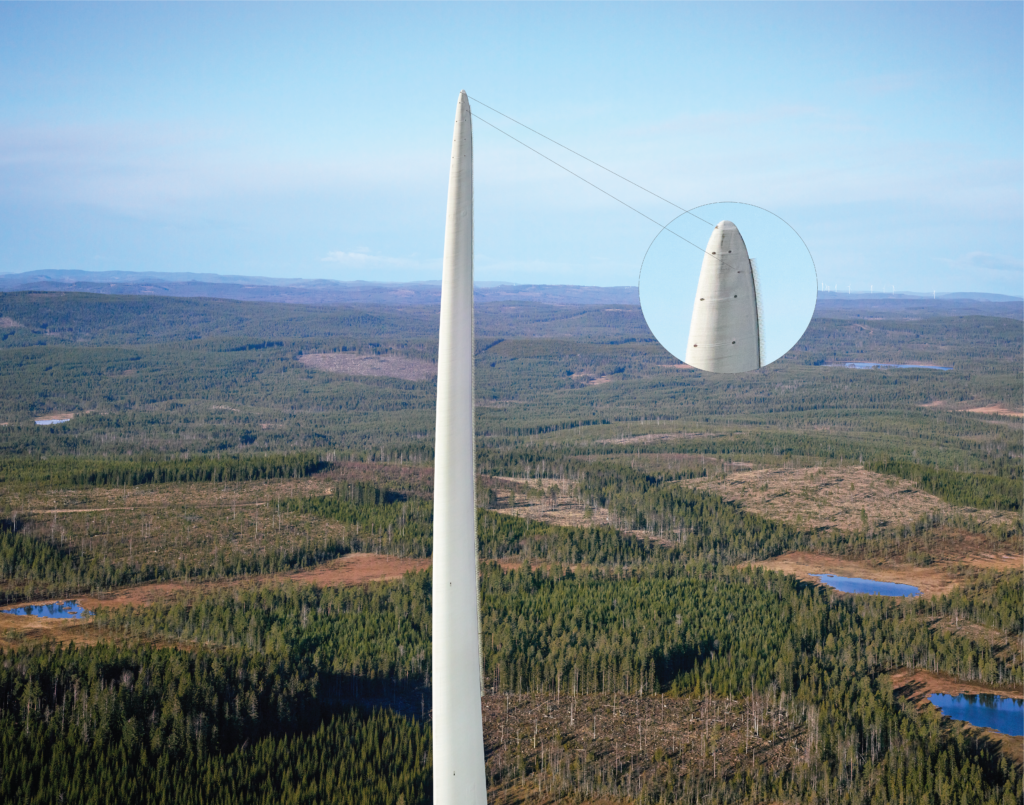
Clear Images of Spinning Blades
The inspection results met high expectations, providing clear images of turbine blades without stopping the turbine.
“The Phase One P3 iXM-GS120 camera allowed us to capture clear, detailed images of wind turbine blades without interrupting operations,” says Jorge Ramos.
The Phase One camera allowed Drone Solution to capture detailed images with 12 shots per blade side, despite challenges from light interference due to the sun being low in the sky.
The DJI Matrice 350 UAV provided excellent stability in windy conditions, with the P3 camera’s stabilizer ensuring images remained free of blur.
After initially testing the system, Drone Solution has identified ways to improve it in future, including a method of labelling the blades to make them easier to distinguish from each other.
The Phase One P3 iXM-GS120 camera allowed us to capture clear, detailed images of wind turbine blades without interrupting operations.
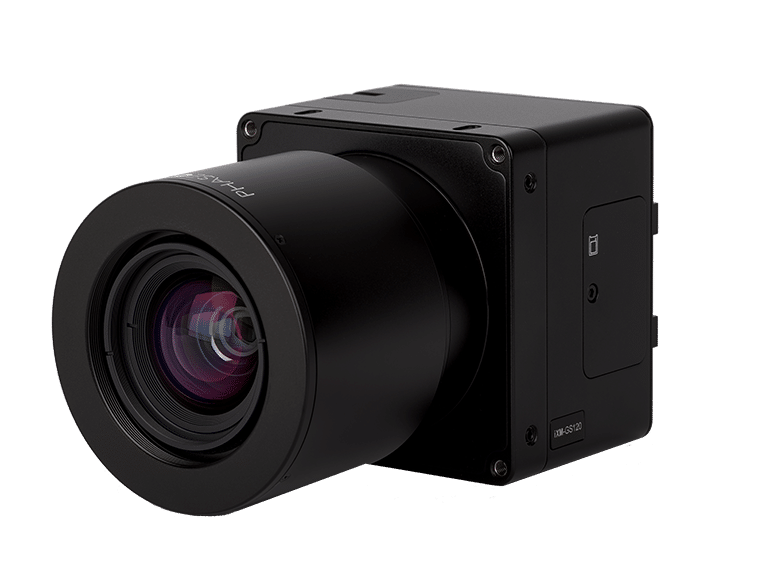
A New Standard for Efficiency?
The Phase One P3 iXM-GS120 camera has enhanced Drone Solution’s inspection capabilities.
By enabling them to consistently capture high-quality images of moving turbine blades, Drone Solution can avoid their clients having to stop operations.
“This improvement has greatly enhanced our inspection process and reduced downtime for our clients,” says Jorge Ramos. “While we are still in the beginning phase, we are confident that with the right software and some adaptations, we can optimize the process even further to deliver even greater efficiency and accuracy.”
In addition to avoiding turbine shutdown costs for their clients, the process is up to 15 minutes faster, increasing their surveying efficiency and reducing inspection time. Moreover, Drone Solution can avoid the need to send engineers to each turbine survey – only the drone pilot needs to be present.
This has the potential to set a new standard for operational efficiency in wind turbine inspections.
Drone Solution’s future goal is to apply the system to offshore wind turbines, where they will be able to increase the efficiency of inspections by performing them from a boat.
About Drone Solution
Drone Solution uses cutting-edge drone imaging technology to enhance inspection efficiency and safety. They specialize in advanced drone-based inspection services for wind turbines, confined spaces, and infrastructure projects including rail, tunnels, and bridges.
See more on the Drone Solutions website.
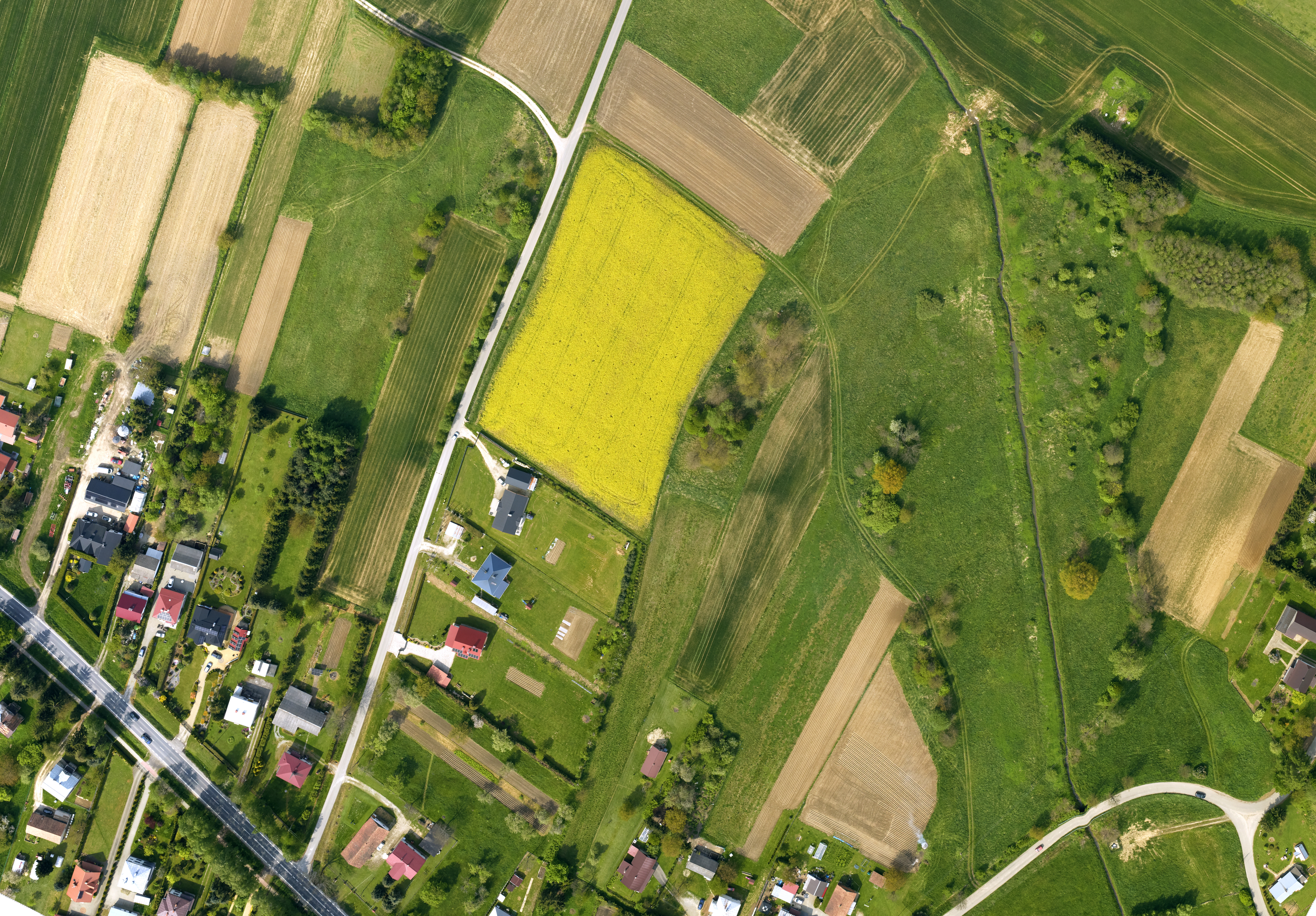
Geospatial
Monitoring pipeline corridor using PAS 280 large format camera
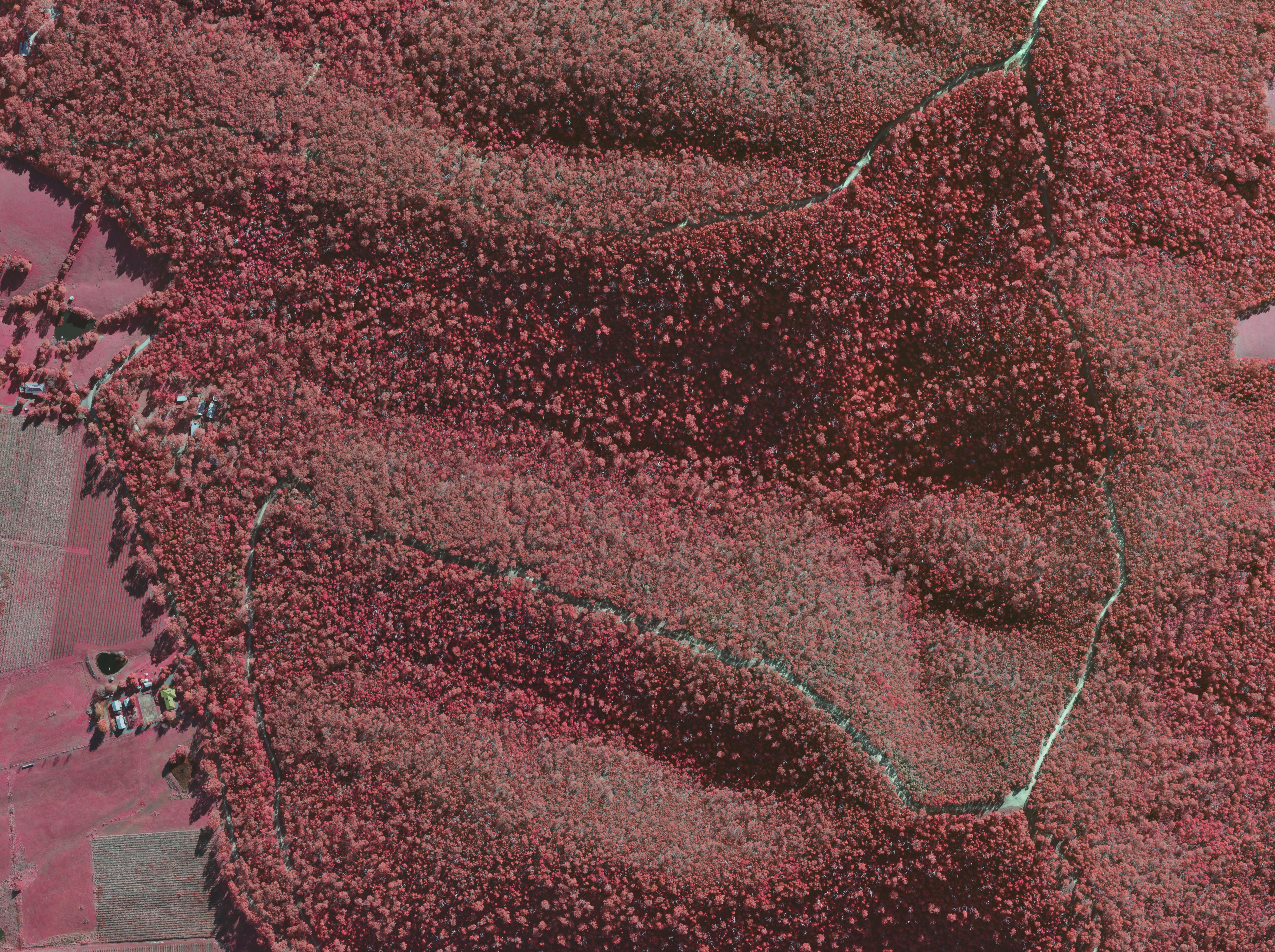
Geospatial
Preventing Wild Bushfires By Mapping Planned Burns
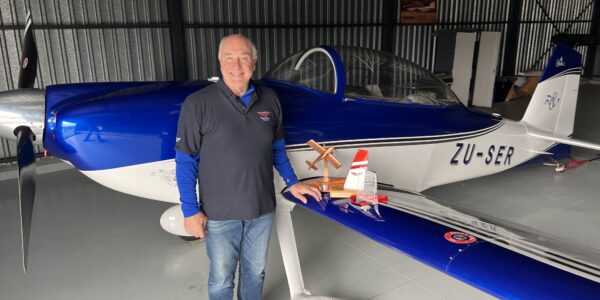
Geospatial
Novice Aerial Photographer Becomes Advanced Mapping Provider
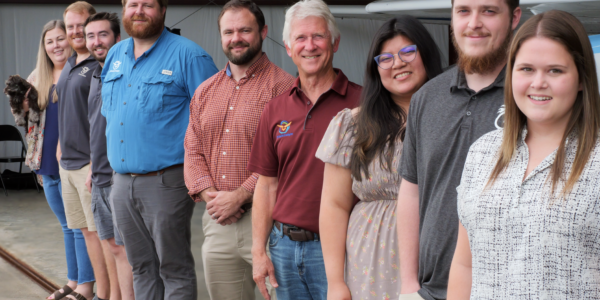
Geospatial
Precision at Altitude: Redefining Aerial Mapping with the PAS 880 Oblique Camera System
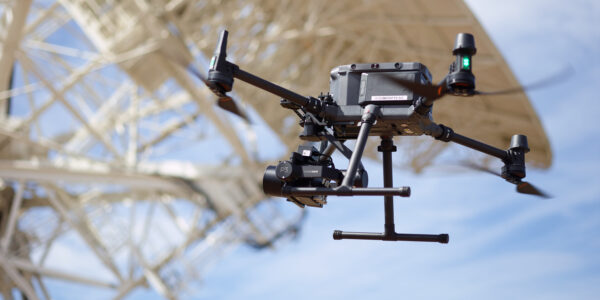
Geospatial
Perfecting telescope dish accuracy with UAV photogrammetry
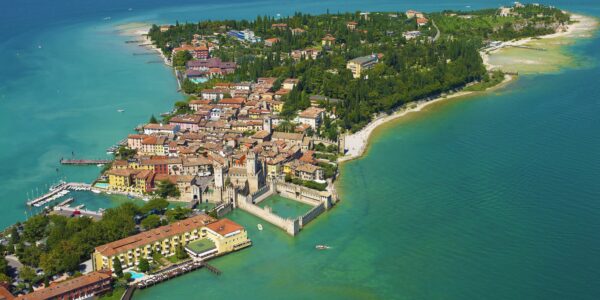
Geospatial
Saving costs while lowering carbon footprint: Innovative aerial surveying service uses small airplanes enabled by compact cameras
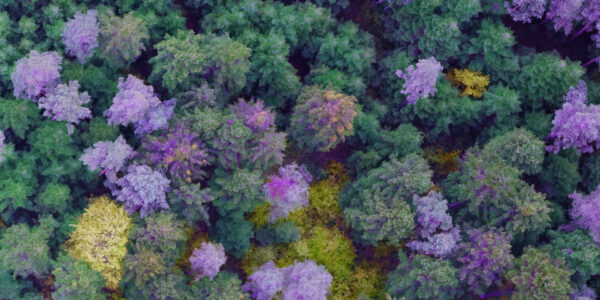
Geospatial
Detecting forest tree diseases using a large-format camera on an ultralight aircraft
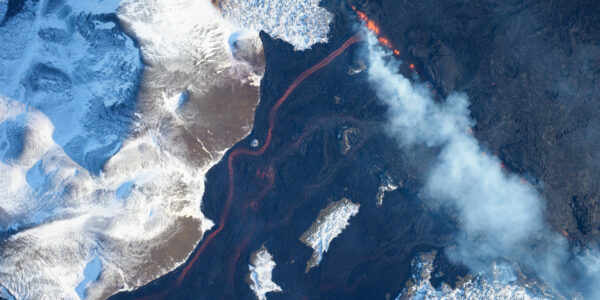
Geospatial
Mapping lava flows during volcanic eruptions in Iceland
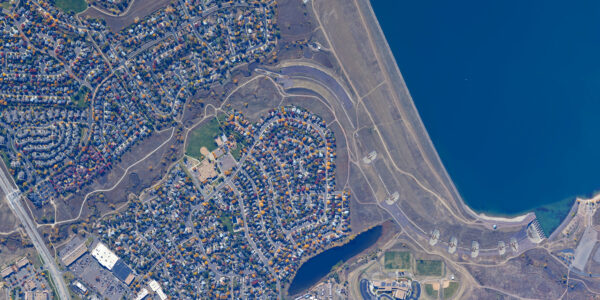
Geospatial
The PAS Pana: a 48,800-pixel camera innovated with our customer Surdex
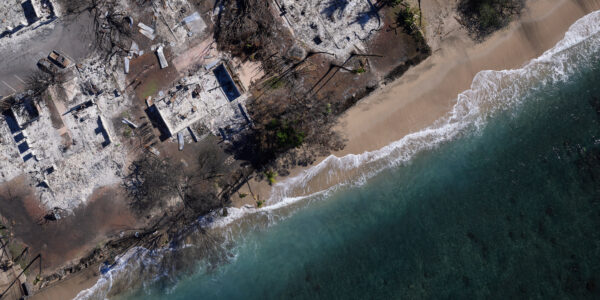
Geospatial
Rebuilding after Hawaii’s wildfire with engineering-grade surveying
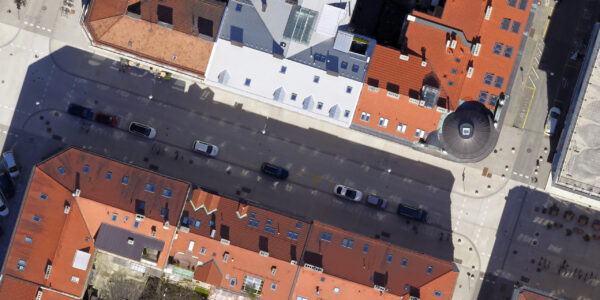
Geospatial
Revolutionizing Slovenian urban planning: Phase One’s PAS 880i redefines reality mapping
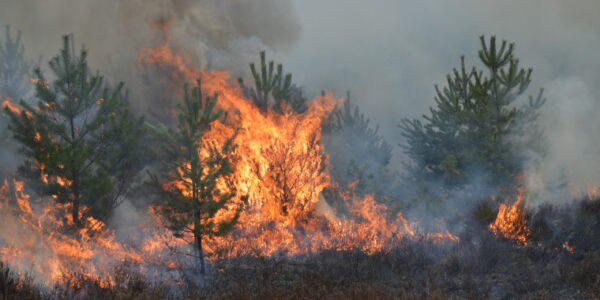
Geospatial
Imaging solutions combined with AI and 5G – A new approach and promising to assess forest health and detect and monitor wildfires
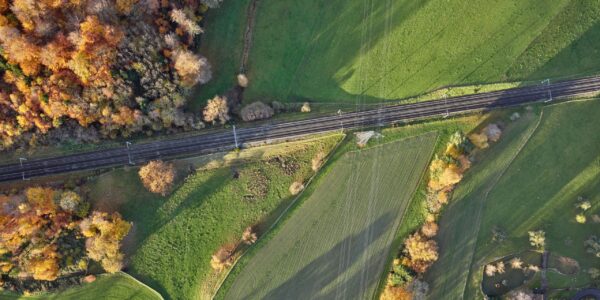
Geospatial
Phase One Cameras combined with light, fixed-wing aircraft deliver highly efficient LiDAR and mapping missions
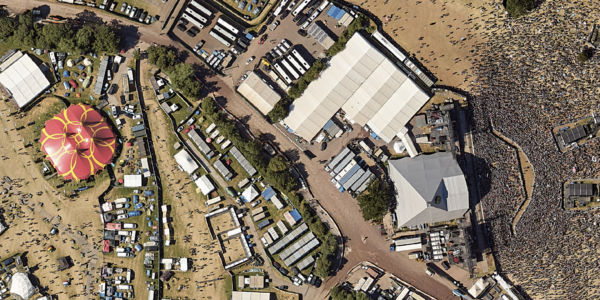
Geospatial
Capturing Glastonbury Festival
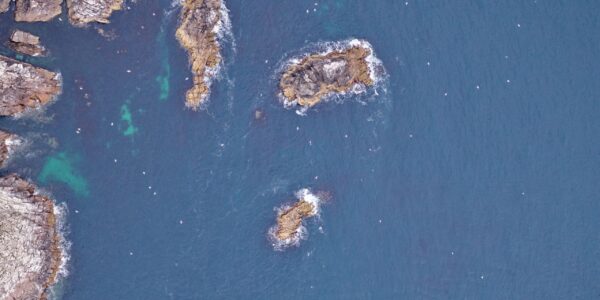
Geospatial
Breaking barriers to offshore wind energy development