The challenge
From 8-9 August 2023 a wildfire raged across the island of Maui, Hawaii, destroying approximately 80% of the town of Lahaina.
Clearing debris and rebuilding the homes, businesses and facilities for the 13,000 people who call Lahaina home is an enormous undertaking requiring coordinated efforts from diverse public and private actors.
To ensure a common operating picture, 8th Axis embarked on an ambitious 3D geospatial model of the town in November 2023, with help from Phase One, Skyline Software, and AeroSpatial data processing. The project used a UAV with a Phase One P3 Payload: an integrated plug-and-play solution for the DJI M300/M350 drone.
8th Axis Industrial LLC (8th Axis)
An industry leader in UAV 3D topographical and architectural scanning based in Honolulu. 8th Axis provides survey management data systems and technology for disaster response, mining, development, solar and wind power, agriculture, and water utilities.
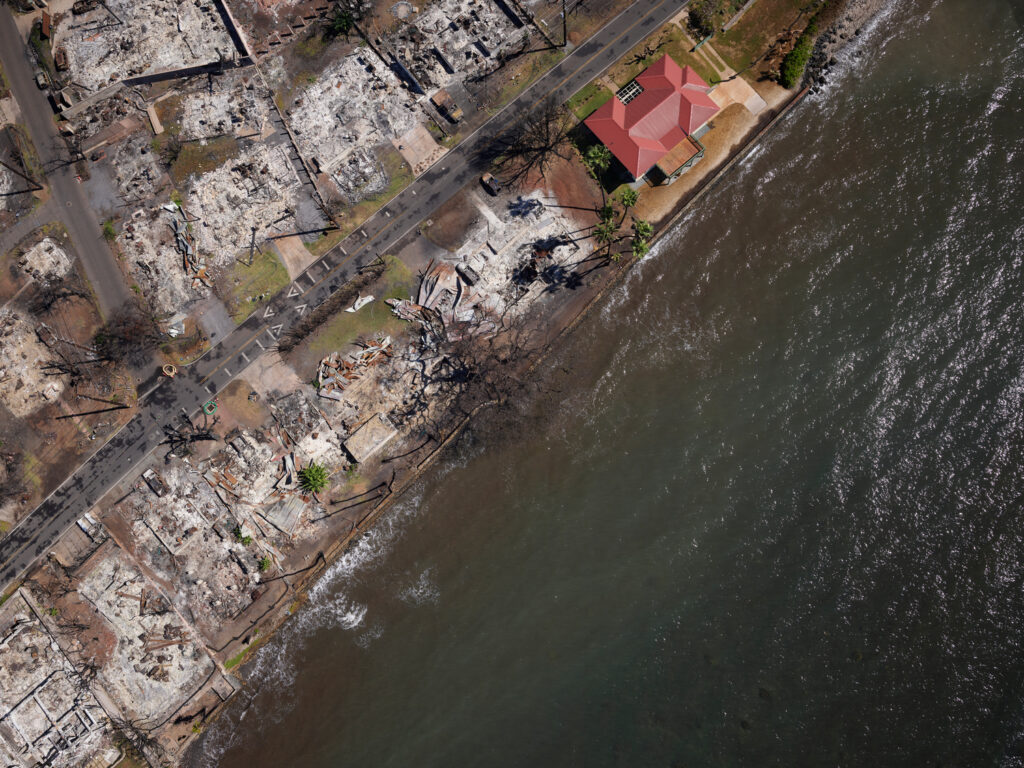
An unprecedented aerial forensic survey
The project began in 2023, aiming to map the entirety of Lahaina to an accuracy of 5 mm Ground Sampling Distance (GSD), over an area of approximately 3,000 acres (1,214 hectares / 12 sqkm).
“As far as we know, nobody has ever done a project of this size, in this resolution – even in the US,” says David Drummond, Business Development Manager at 8th Axis.
The ultra-high-resolution imagery has given the team the capability to reconstruct Lahaina in a 3D mesh model with data layering. This geospatial environment is rendered in an unrivalled level of detail, with well-defined geometry.
“When we take screenshots from the 3D mesh, people can’t distinguish between the mesh and an actual photograph,” says David. “We call it a forensic aerial survey because the level of detail is so high that you can actually zoom in and inspect it remotely.”
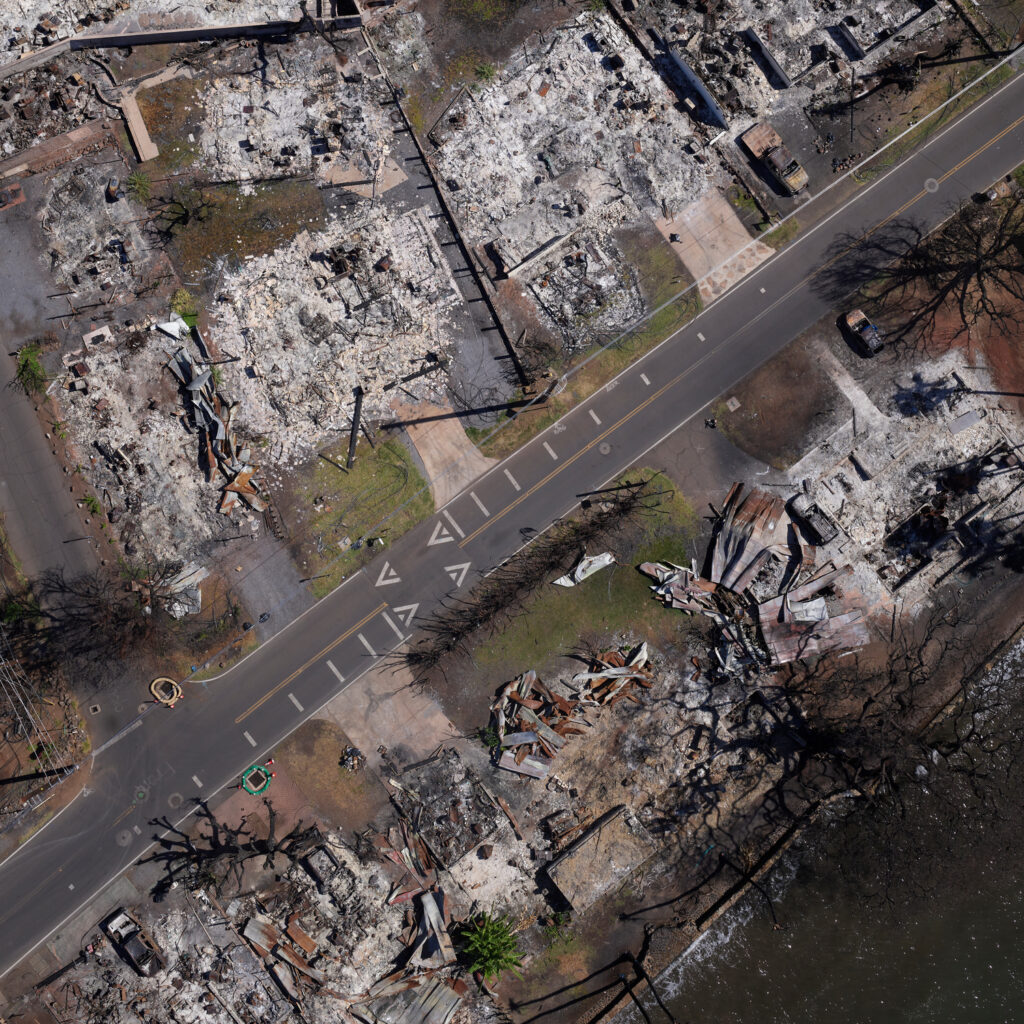
Helping safer, more efficient recovery efforts
Having a single source of baseline information in an easy-to-understand visual format helps the many agencies and interests at work to coordinate and share effectively.
It helps the Hawaii Emergency Management Agency (HEMA) to interact with county, state, federal, and private industry partners. These various agencies can work together to plan relief and response efforts, share notes, and then remotely inspect areas, individual properties, and even individual piles of debris – without having to expose people to potentially toxic and dangerous environments.
According to HEMA Administrator James Barros: “Having a clearer image of this disaster scene is an exciting development for emergency managers.”
“3D imaging helps to provide triage for the areas in question, while at the same time maximizing resources and experts,” he says.
An example of this is the hydrology model, which helped the emergency teams select effective barrier placements to contain runoff from burn scars in the event of heavy precipitation.
Ground control was supplied by Fukumoto Engineering, and local Maui firm.
What is the data used for?
A photorealistic 3D mesh and a suite of geospatial data products including a pointcloud, orthomap, DSM, DTM, contours, and hydrology model, with a level of detail and definition not seen before.
These are used for remote inspection, asset management, automated volumetric change detection, and Virtual Design and Construction (VDC).
In future, the data will be sold as a subscription-based service to other government and commercial entities such as ArcGis, with quarter-annual updates.
A certified engineering–grade aerial survey
The photogrammetry data has been signed off and accredited by a licensed surveyor, making it a formal survey with data validated to engineering-grade accuracy. It meets and even exceeds the Accuracy Standards for Digital Geospatial Data (ASDGA) from the American Society for Photogrammetry and Remote Sensing.
This means designers and engineers can bring the 3D mesh into a CAD program and rebuild Lahaina’s buildings and infrastructure using the 3D mesh as the base file.
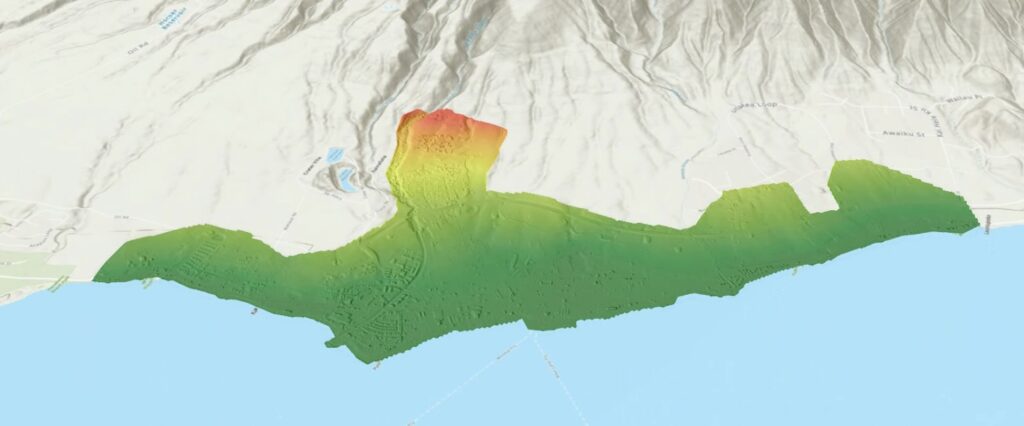
Precise, independent volumetric measurements
Such geospatial accuracy allows for precise measurements of structures and debris piles within the 3D model. With 8th Axis updating the survey as necessary over the next three to five years, they can compare different surveys against each other.
For this, they use AI-powered volumetric change detection, which gives highly accurate analytics of changes in topography and volumes of the debris being removed. This allows government stakeholders to track these factors independently of reporting by contractors and subcontractors. It also enables government entities such as the U.S. Army Corps of Engineers to maintain greater awareness of how their timeline is moving toward the next stage. Together with better cost auditing, this helps keep costs down and allows for better overall coordination and planning.
Accuracy in baseline and subsequent surveys is critical to the longevity and relevance of this dataset.
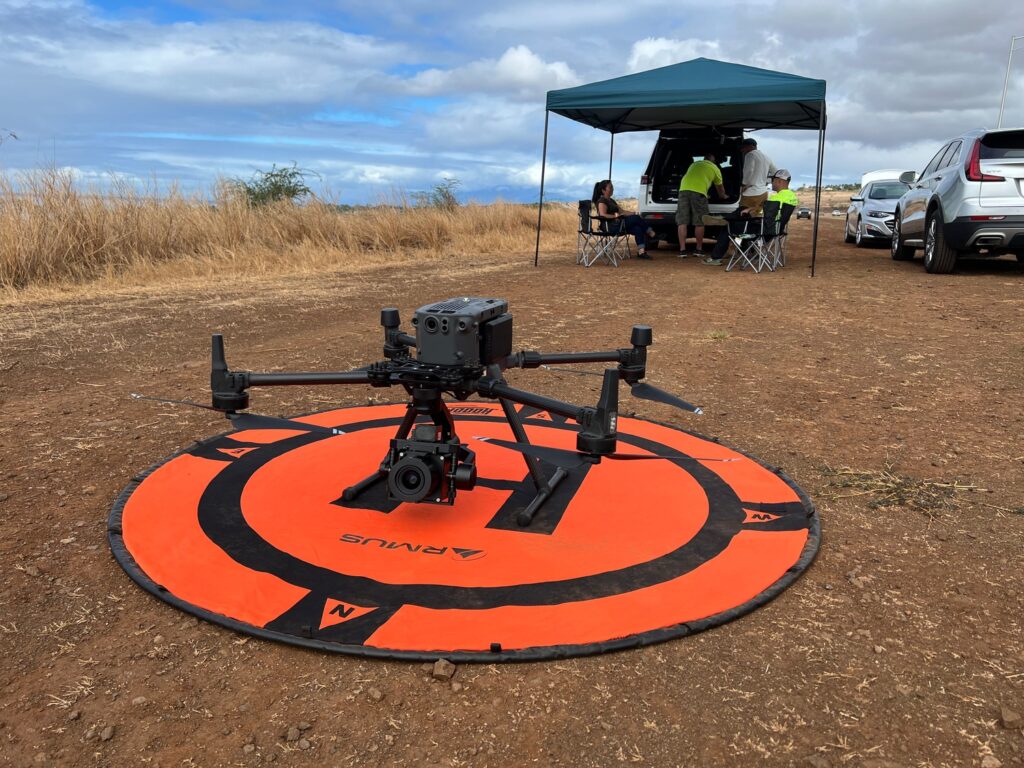
Phase One accuracy at speed gives robust data
Using a Phase One P3 payload with a 35 mm lens gave the team the capability to reach their target GSD of 5 mm.
The P3 integrates easily into a DJI M300/M350 drone, allowing the team to cover the entire 3,000-acre project area with precise overlap and speed when using automated nadir survey patterns.
The P3 allowed us to capture data much faster than other cameras while still providing a GSD that far exceeds that of other cameras when flown at the same altitudes and speed.
In total, the team spent five days, during which time they captured the imagery in different ways, essentially covering the 3,000-acre area twice.
David believes that a top Commercial Off The Shelf (COTS) industrial camera would have taken them 10 days and the product would have been 40% of what they actually achieved.
Photogrammetry was far more efficient than a Lidar survey too, which the team had previously undertaken near Lahaina in 2020. “A 500-acre area took five days to capture, and was phenomenally expensive to process compared to photogrammetry,” says David.
Because the P3 reduced the time needed, it enabled more robust data capture in a scenario where debris and ash are continuously moving with recovery operations. It also avoided the common issues of changing lighting conditions and other environmental factors that usually affect UAS data collection over large areas.
“We ended up with a flawless, contiguous data set that we would have struggled to achieve with other sensors,” says David.
Rowland Harrison of AeroSpatial adds: “That is possible only because the camera itself has such a wide field of view in such a high resolution that we can fly faster. That efficiency is key.”
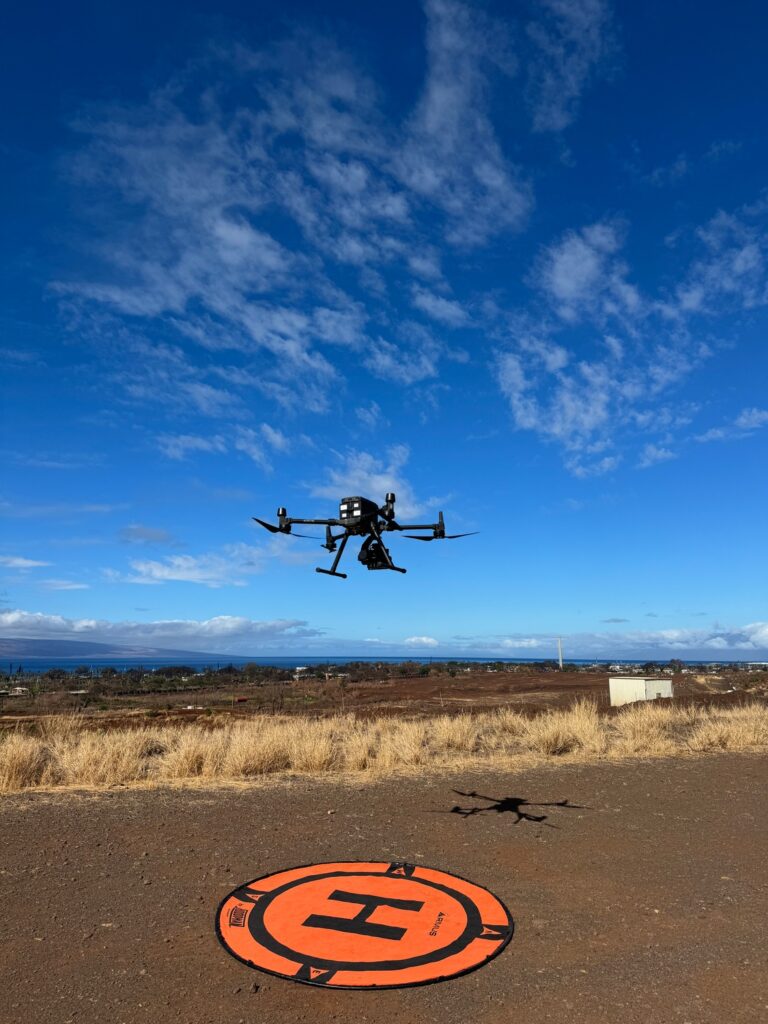
Infinite focus is critical
Being able to set the camera’s focus to infinity was essential to the project’s success. Cameras without this capability must autofocus before each image, preventing them from shooting as quickly as the P3. This results in missed images and a lack of image overlap.
Getting infinite focus right is a critical component for Rowland Harrison. “There is a difference between ordinary camera manufacturers and those who make cameras for aerial use; there is a lot of complexity,” he says.
“The P3 itself is just phenomenal,” continues Roland. “It has a very good sensor. All the images are really sharp, and that allows us very accurate feature matching and photogrammetry. I wouldn’t have expected anything less from Phase One.”
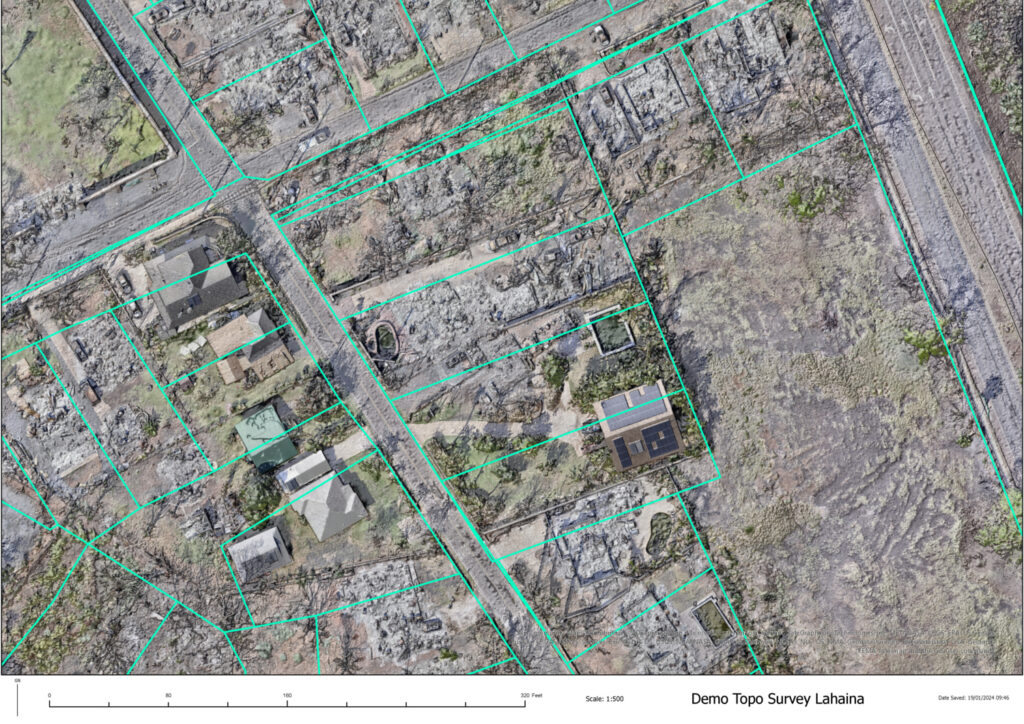
Making varied lighting look like one
Pre-production color balancing with Capture One software was essential for the aerial forensic survey’s success. It enabled seamless 3D mesh creation despite diverse shooting conditions over five days, achieving consistent lighting even in low-light situations.
What the future has in store
8th Axis and the team are aiming to perform up to 13 resurveys as needed – biannually or quarterly – for at least three years following the initial survey.
In wider terms, the team strongly believes that this project with its geospatial data set, when paired with their ground control and the resulting analysis from the planned updates, will redefine the standards for aerial surveys on a global scale.
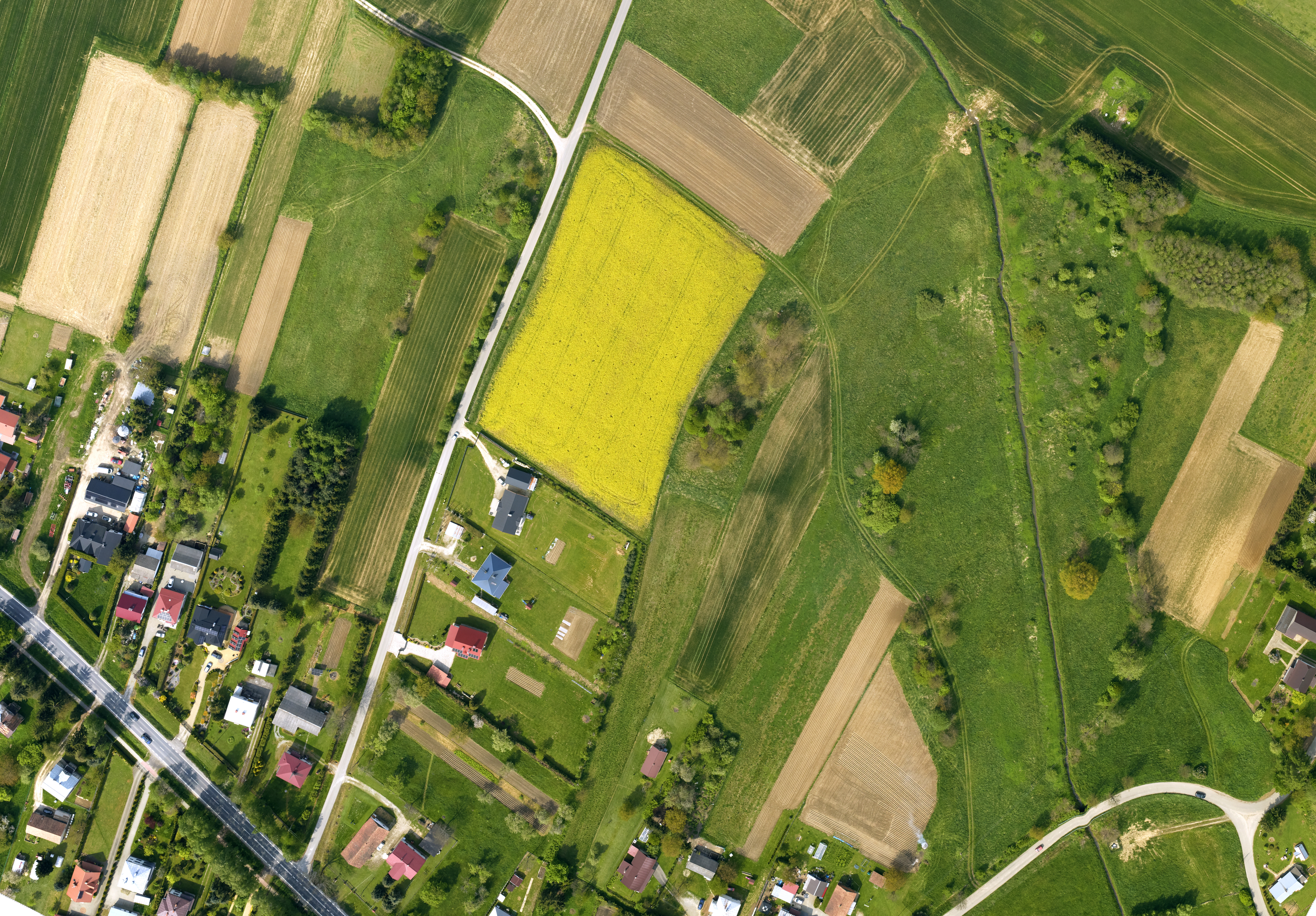
Geospatial
Monitoring pipeline corridor using PAS 280 large format camera
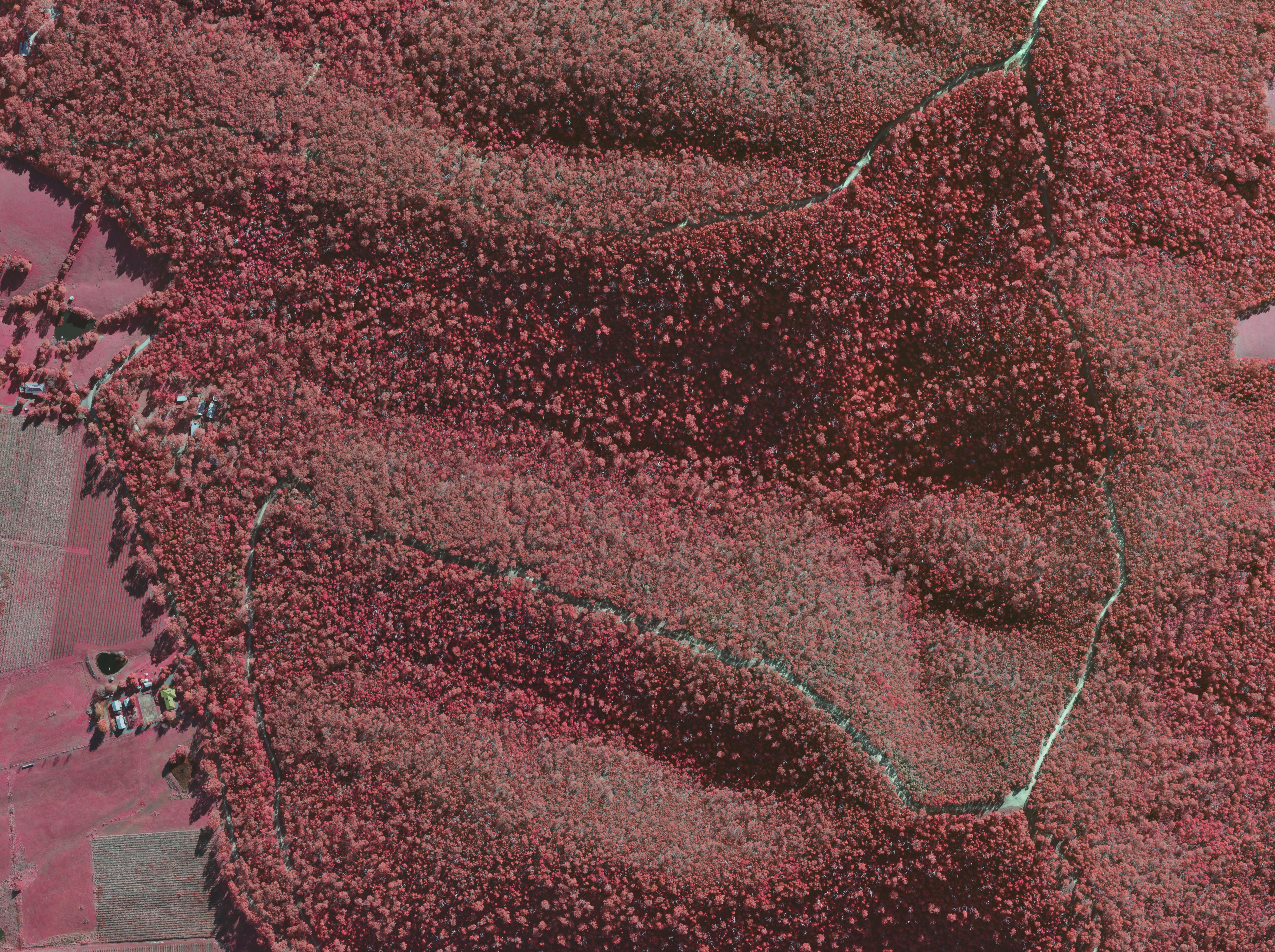
Geospatial
Preventing Wild Bushfires By Mapping Planned Burns
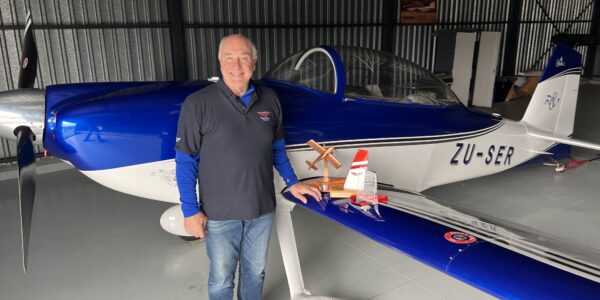
Geospatial
Novice Aerial Photographer Becomes Advanced Mapping Provider
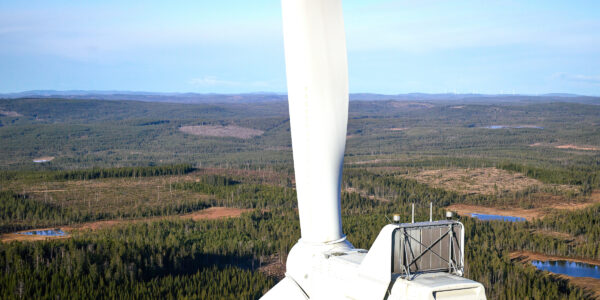
Geospatial
Inspecting Wind Turbine Blades While They Are Rotating
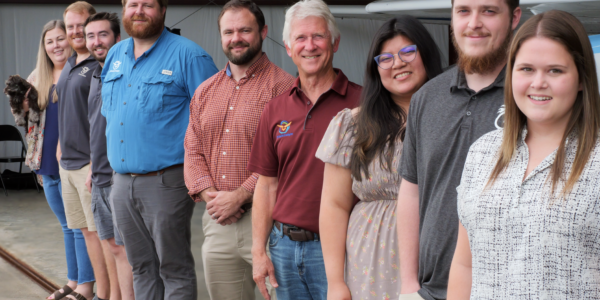
Geospatial
Precision at Altitude: Redefining Aerial Mapping with the PAS 880 Oblique Camera System
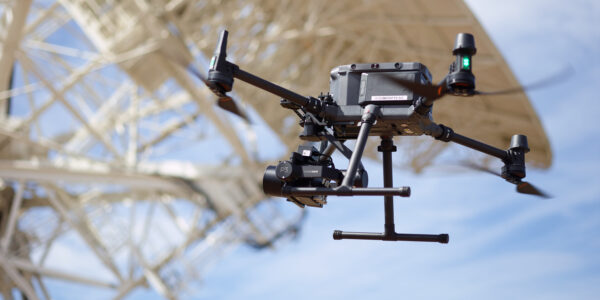
Geospatial
Perfecting telescope dish accuracy with UAV photogrammetry
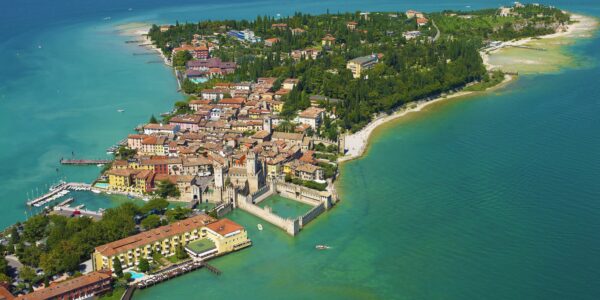
Geospatial
Saving costs while lowering carbon footprint: Innovative aerial surveying service uses small airplanes enabled by compact cameras
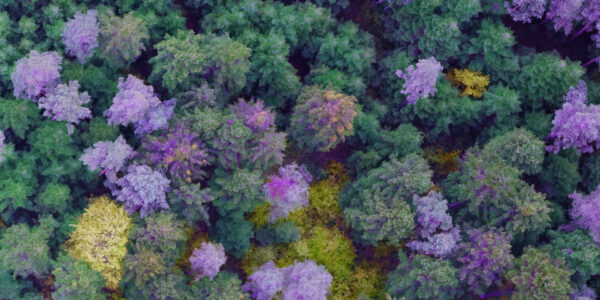
Geospatial
Detecting forest tree diseases using a large-format camera on an ultralight aircraft
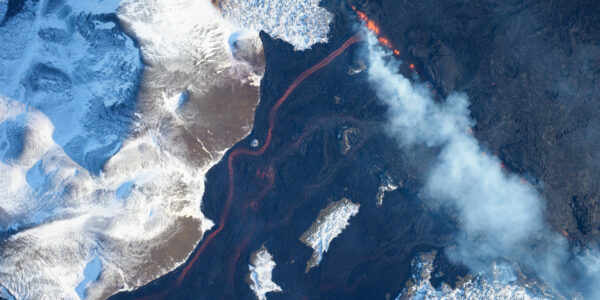
Geospatial
Mapping lava flows during volcanic eruptions in Iceland
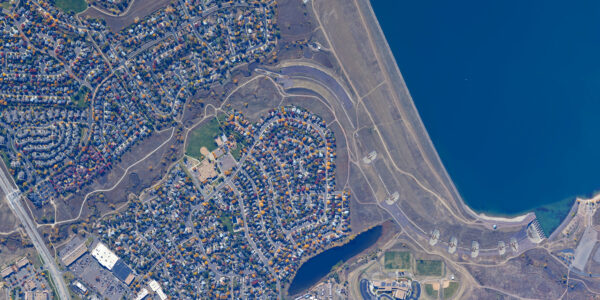
Geospatial
The PAS Pana: a 48,800-pixel camera innovated with our customer Surdex
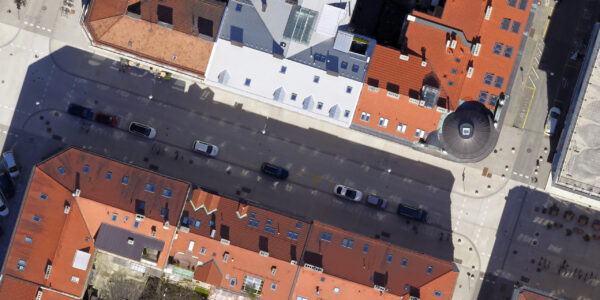
Geospatial
Revolutionizing Slovenian urban planning: Phase One’s PAS 880i redefines reality mapping
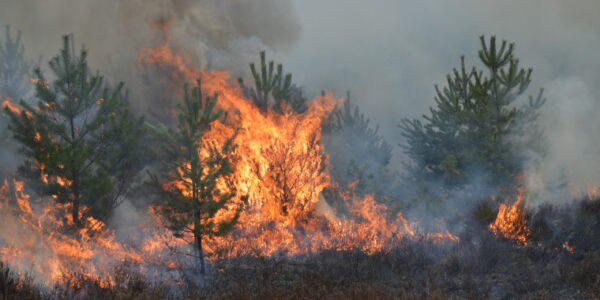
Geospatial
Imaging solutions combined with AI and 5G – A new approach and promising to assess forest health and detect and monitor wildfires
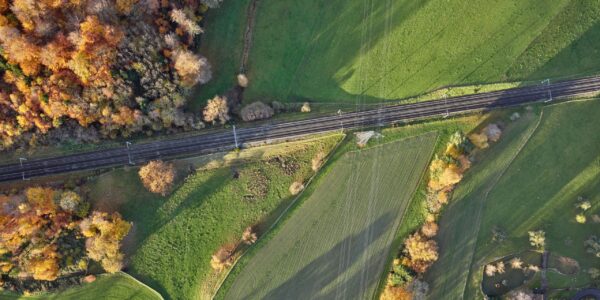
Geospatial
Phase One Cameras combined with light, fixed-wing aircraft deliver highly efficient LiDAR and mapping missions
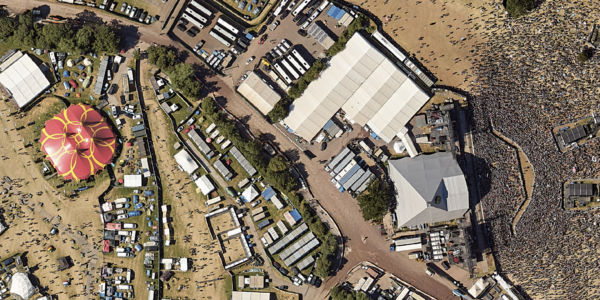
Geospatial
Capturing Glastonbury Festival
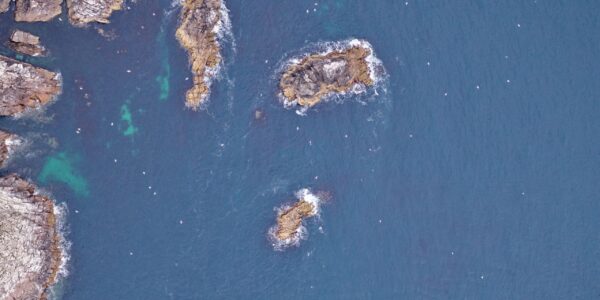
Geospatial
Breaking barriers to offshore wind energy development