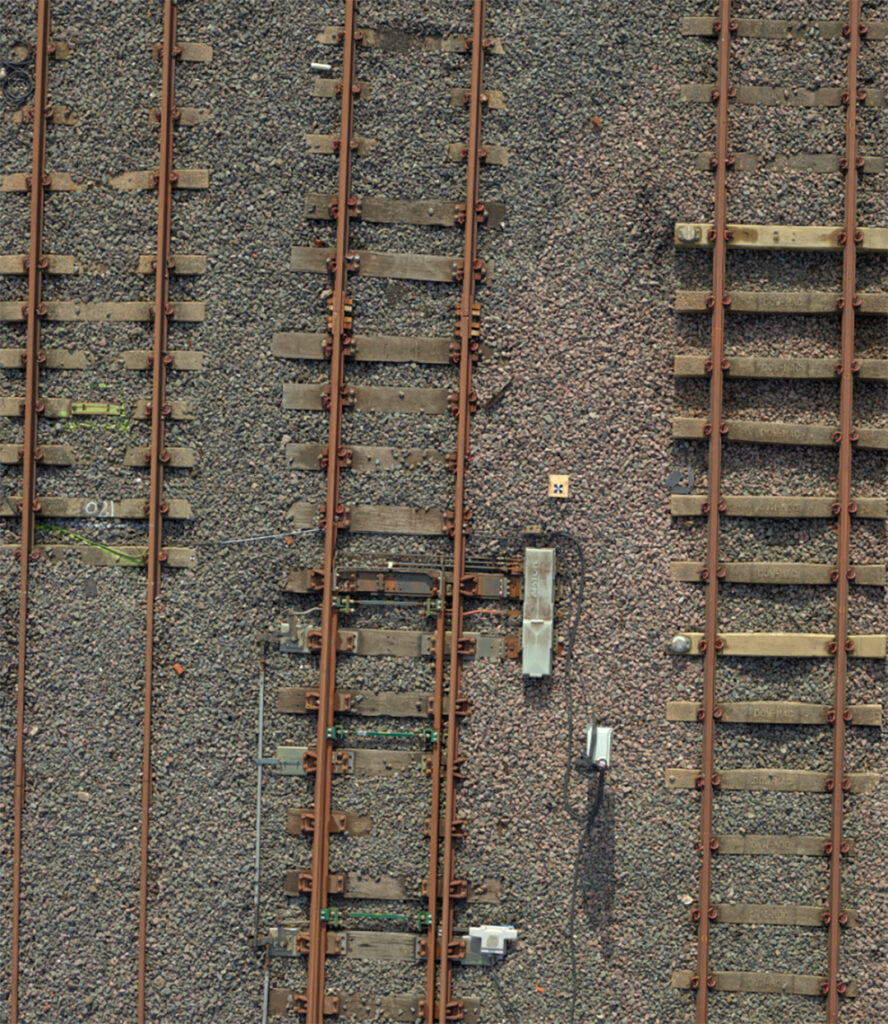
Creating a “Digital Railway”
One of the major challenges that railway networks are facing is prevention of failures in railway tracks. The task of inspecting thousands of miles of tracks stretching across the land, especially with drone infrastructure inspection, must be performed with speed, efficiency and safety to avoid risk and traffic interference.
An innovative methodology of railway inspection is by creating a “digital railway” – an accurate and dynamic visualization tool, for fast and accurate potential damage identification, enabling professionals to take informed decisions while planning and prioritizing rail development, maintenance, repairs and renewal projects.
Recently, the use of drone-based platforms in the aerial imaging market is increasing rapidly, and remote sensing is becoming a preferred method for acquiring qualitative aerial data. These platforms offer easy and safe aerial access to challenging areas, a larger surface coverage in a single flight, higher resolution images, and efficient, cost-effective aerial data acquisition.
Plowman Craven is a measurement survey company that specializes in providing laser scanning, surveying, and measurement data services, to both public and private sectors. Having spent many years conducting railway track surveys for Network Rail, and recently created a world-first technical solution for Cross rail, Plowman Craven’s Rail team spent more than two years researching whether the drone surveying and inspection capabilities used for buildings surveys, rooftops and landscapes, could be applied to the rail environment.
The application of the Vogel R3D system is a real game-changer for Network Rail and helps us to satisfy many of our survey requirements in a safe manner without the cost implications or potential programme delays associated with multiple possessions.
Vogel R3D – Expanding Rail Infrastructure Surveying Accuracy
In collaboration with Network Rail, Plowman Craven developed the Vogel R3D – a drone-based system with an integrated Phase One 100MP medium format camera, that enables comprehensive surveying and inspections of rail infrastructure to a sub-5mm accuracy from a height of 25m. The system captures overlapping aerial images of an entire site that are then converted into high-accuracy 3D data by bespoke software and algorithms.
The reasons to integrate Phase One’s 100MB camera were the fact that it is the lightest weight camera in its category, the large sensor that captures large amounts of light and improves data quality, and the high dynamic range that enables accurate capture of high and low-intensity objects.
With enhanced permissions and an ‘Operation Safety Case’ from the Civil Aviation Authority, Plowman Craven’s UAV team is able to fly at a low altitude, closely inspecting live railways. Operating at a height of 25m, Vogel follows a series of pre-programmed flight paths to capture hundreds of overlapping high-resolution images using Phase One’s 100MP Aerial Camera.
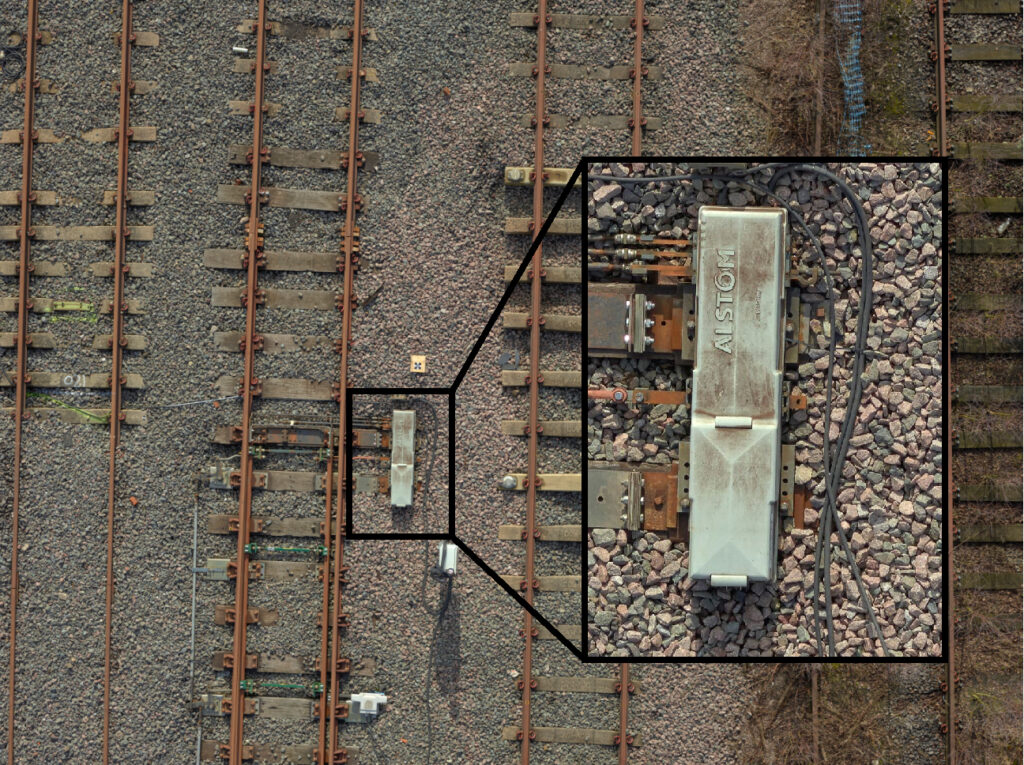
Ultra High-Resolution Imagery
The Vogel R3D covered 10,000 square-meter sites in 6 hours of air time with no return visits required. The ultra high resolution imagery enabled the generation of high-accuracy survey-grade data and ensured a complete visual record that is backed up by measurement data. The superb quality of the raw photography captured enables the study of the smallest markings on the sleepers, identification of specific rail clips and makes it possible to clearly view flash butt welds – objects that are highly problematic for surveyors when working on the tracks at night.
The value of this visualised data is significant. It enables stakeholders to ‘walk’ the site from anywhere in the world using a tablet or computer, making imagery interrogation and the extraction of measurements possible. The high level of detail and the accuracy of the extracted data supports decision-makers in monitoring, planning, predicting and preparing for railway maintenance projects in an efficient, safe and cost-effective manner.
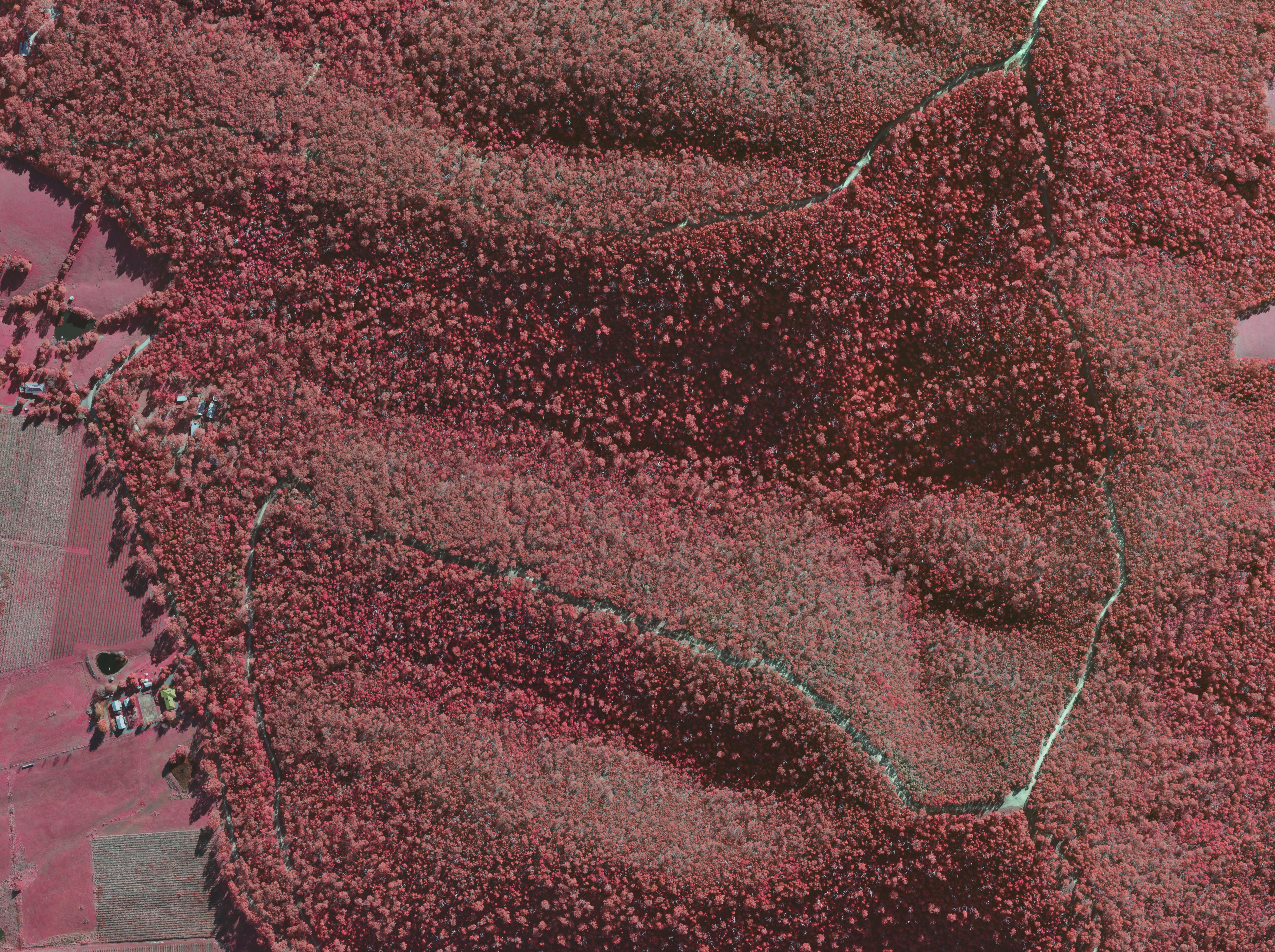
Geospatial
Preventing Wild Bushfires By Mapping Planned Burns
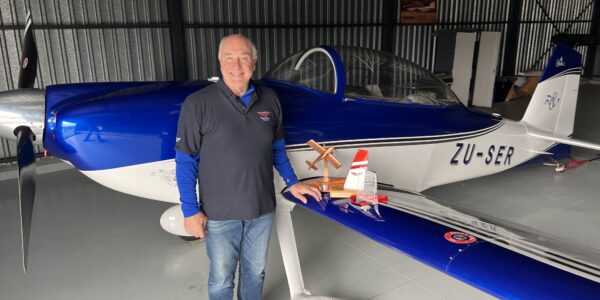
Geospatial
Novice Aerial Photographer Becomes Advanced Mapping Provider
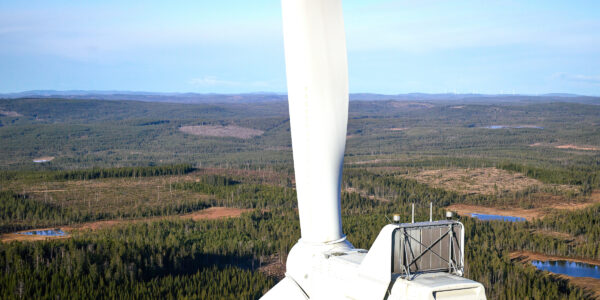
Geospatial
Inspecting Wind Turbine Blades While They Are Rotating
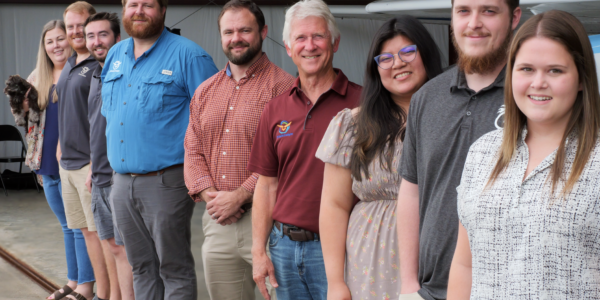
Geospatial
Precision at Altitude: Redefining Aerial Mapping with the PAS 880 Oblique Camera System
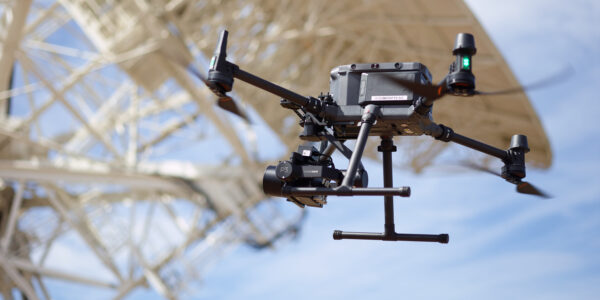
Geospatial
Perfecting telescope dish accuracy with UAV photogrammetry
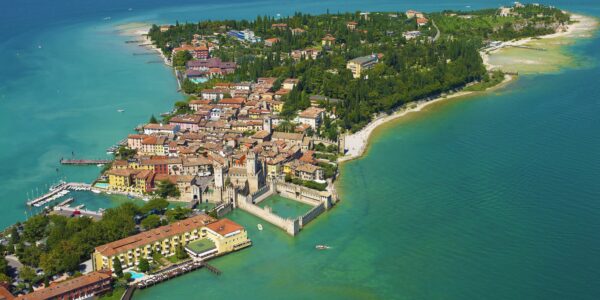
Geospatial
Saving costs while lowering carbon footprint: Innovative aerial surveying service uses small airplanes enabled by compact cameras
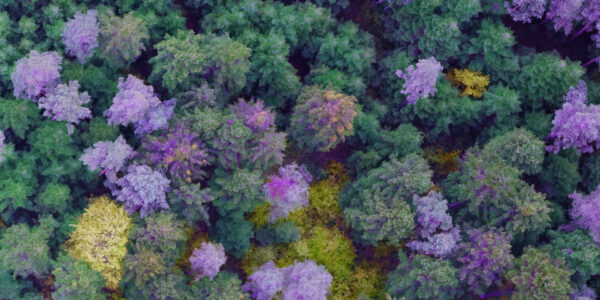
Geospatial
Detecting forest tree diseases using a large-format camera on an ultralight aircraft
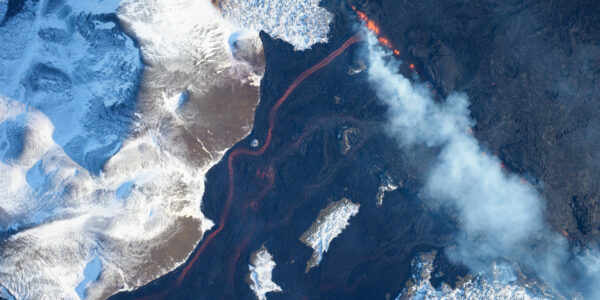
Geospatial
Mapping lava flows during volcanic eruptions in Iceland
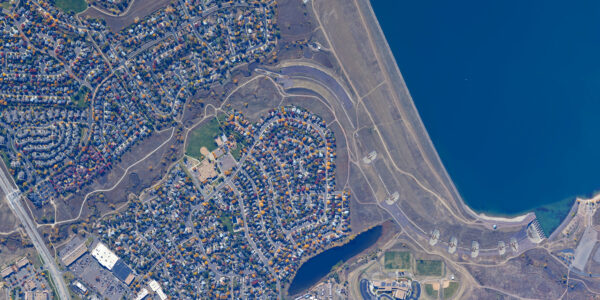
Geospatial
The PAS Pana: a 48,800-pixel camera innovated with our customer Surdex
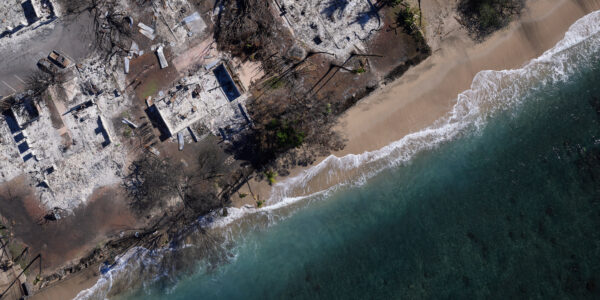
Geospatial
Rebuilding after Hawaii’s wildfire with engineering-grade surveying
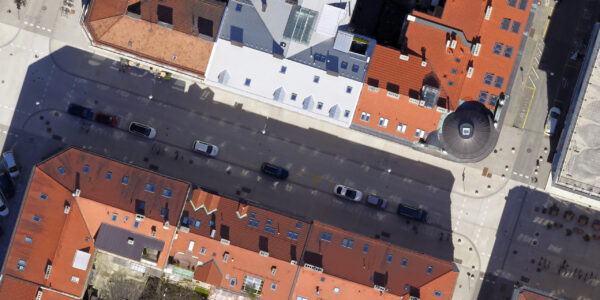
Geospatial
Revolutionizing Slovenian urban planning: Phase One’s PAS 880i redefines reality mapping
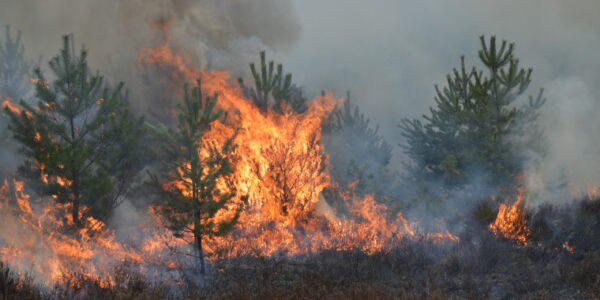
Geospatial
Imaging solutions combined with AI and 5G – A new approach and promising to assess forest health and detect and monitor wildfires
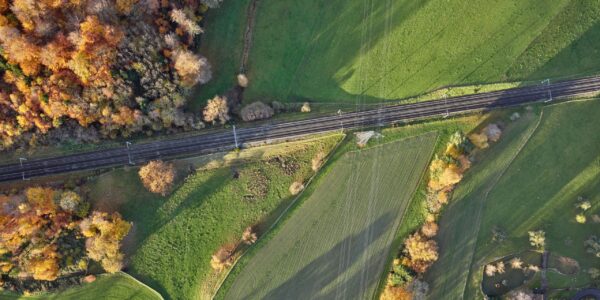
Geospatial
Phase One Cameras combined with light, fixed-wing aircraft deliver highly efficient LiDAR and mapping missions
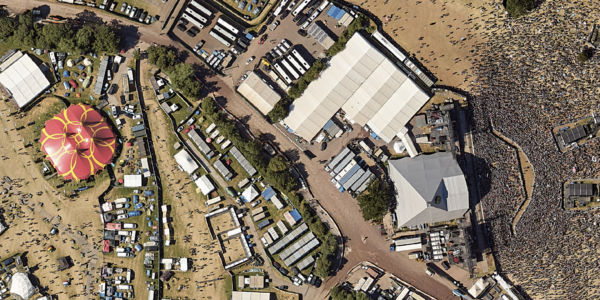
Geospatial
Capturing Glastonbury Festival
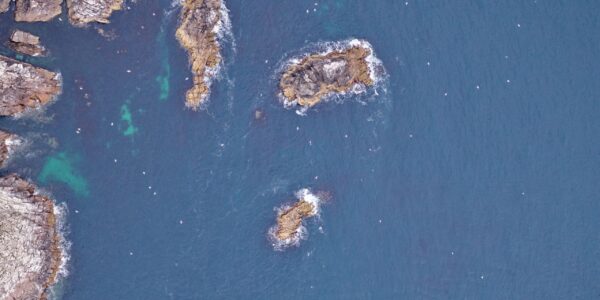
Geospatial
Breaking barriers to offshore wind energy development
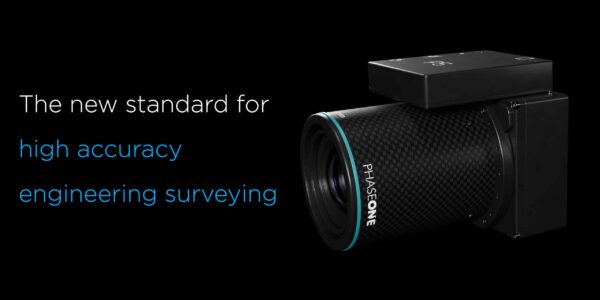
Press Release
Phase One, Quantum Systems and Trimble unveil groundbreaking survey grade UAV solution with the launch of Phase One P5 camera
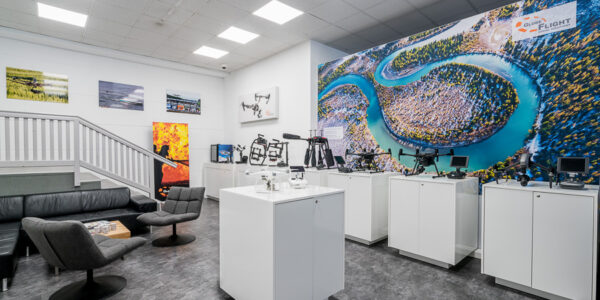
Geospatial
Phase One Selects Globe Flight as Sales Partner for Drone Solutions in Germany and Austria
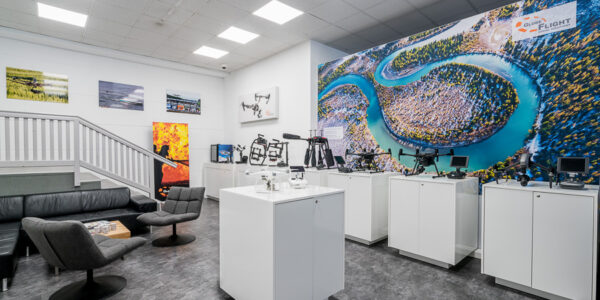
Press Release
Phase One ernennt Globe Flight GmbH als Vertriebspartner für Drohnenlösungen in Deutschland und Österreich
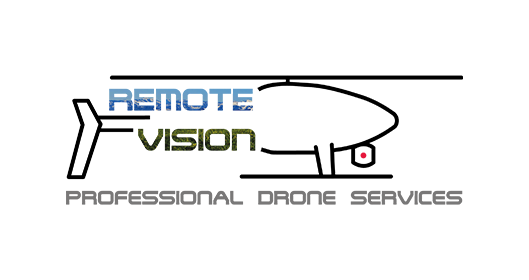
Press Release
Remote Vision Named as Swiss Reseller of Phase One Drone Payloads